The sculling oars are finished and ready to be fitted to the boats. My dad gave me a large block of wood that he had laying around to use as the oarlock. The oar on Wisdom (1968 Morgan 45) is 16 feet long, while the oar on Windpuff (1966 Alberg 30) is 14 feet long.
The oarlock needs to accomplish various tasks:
Needs to hold the sculling oar in place
Needs to allow free movement of the sculling oar
Needs to raise the sculling oar enough so that it doesn't hit the traffrail.
Windpuff has no traffrail (a future project) so there is less in the way of the oar. The future traffrail can be made to clear the sculling oar, so it is not a concern for placement right now.
Wisdom on the other hand has a rather wide traffrail, so I need to be certain that the sculling oar will not damage the teak. For this reason, the oarlock will be made much higher on wisdom.
I oriented the grain so that the oar will rest closer to the heartwood and the cleats that will hold the lashings will be placed on the sides where the grain is closer to 45 degrees so the screws would have good holding.
The corners will be bullnosed and the heart section dished out to help restrain the sculling oar. The base will be bedded and lag bolted to the deck from underneath.
You can see how the oarlock needs to gain enough height to clear all the stern fittings. While the top will be dished a bit, it will still provide enough height to clear the edge of the traffrail.
By looking at the grain of the wood, I believe it is longleaf pine. This wood used to be used to build boats in the early 1900s and has moderate rot resistance. The most important part of keeping this wooden piece healthy will be to maintain the coating and keep it oiled. This will keep moisture out which will prevent rot and mold from setting in. Exposure to salt will also help pickle it and keep the wood hydrated. I plan to design the oarlock so that it will shed water and keep itself dry. Standing water will lead to rot, so keeping up on the maintenance will be crucial to the longevity of the wood on board.
The next issue is storage of the long oars. I plan to keep them tied to the lifelines, away from the sheets and out of the way. For now, they are laying on the decks until their homes can be found
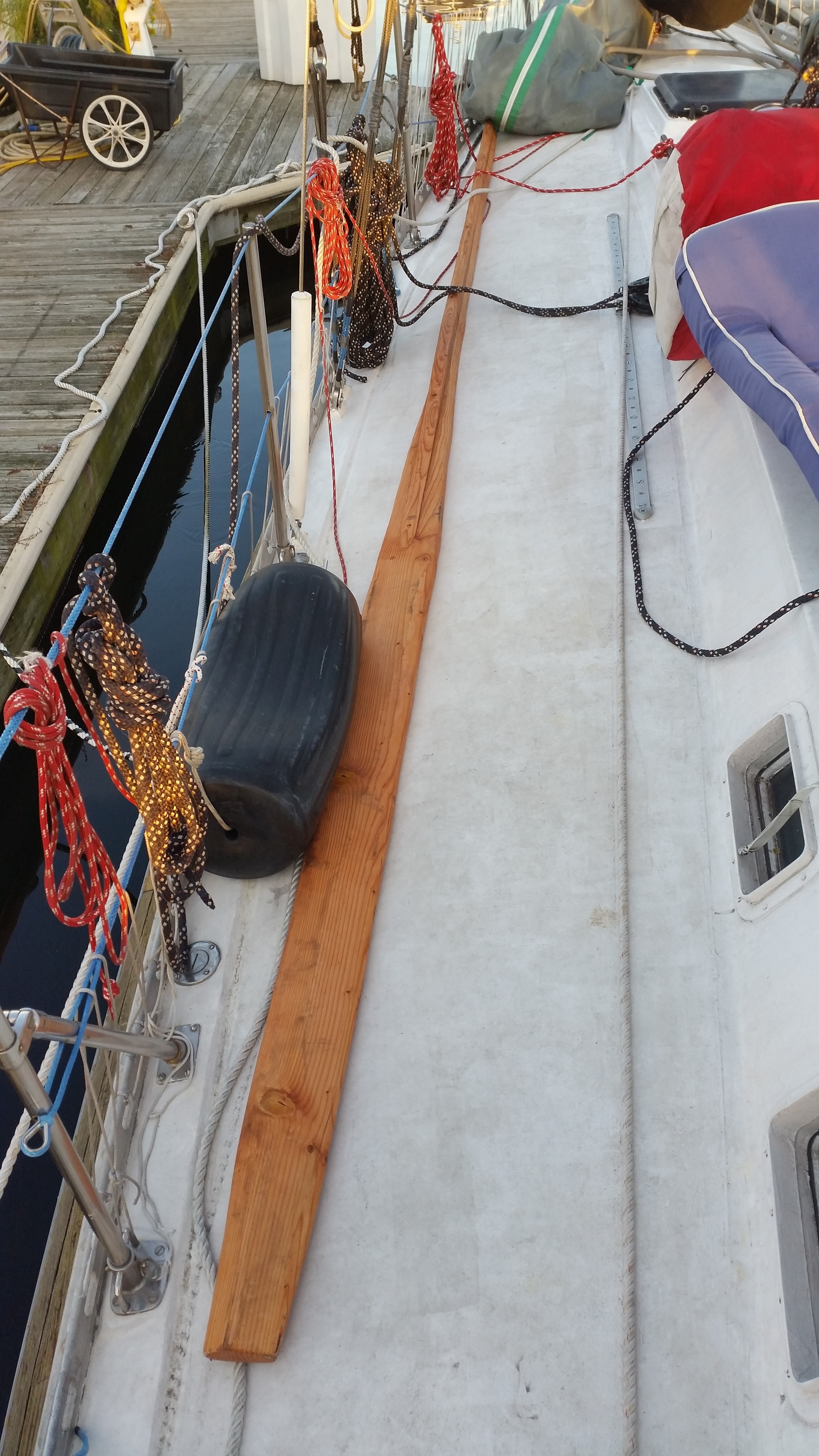
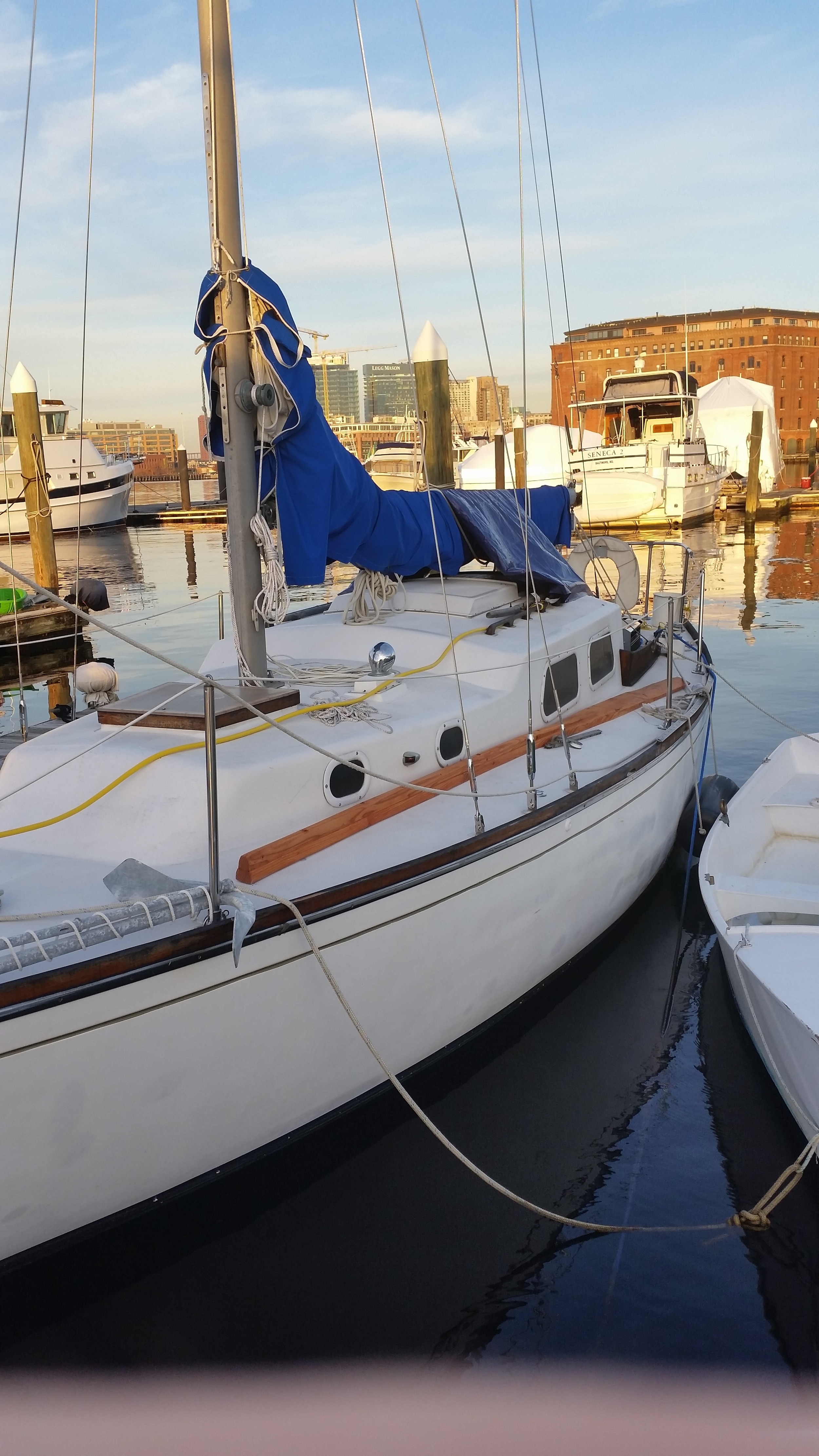